Wool as a Bonding Agent:
Exploration of New Fabrication Methods
Design for Manufacture programme
Research Partner - Ou Yang Chun-Nien
The Bartlett School of Architecture, UCL, 2018
The tactile qualities of materials are central to the way one interacts with their environment.
The main aim of the research is to reintroduce a novel role for soft materials in the architectural realm. It seeks to re-examine wool’s inherent ability to consolidate and transform into felt.
The study explores the potential of wool as a bonding agent, and the felting process as a binding operation via advanced fabrication tools. The new material practice intends to form a methodology where wool is implemented in diverse scenarios, to enrich the architectural space and enhance its tangible qualities.
The project focuses on a widely used, yet rarely glorified material: wool.The organic fibre is known for its remarkable qualities. It is biodegradable, non-flammable,temperature regulating and can absorb toxic chemicals to mention but a few. The study specifically focuses on wool’s unique characteristics and investigates previously untested applications of the material.
The main aim of the research is to reintroduce a novel role for soft materials in the architectural realm. It seeks to re-examine wool’s inherent ability to consolidate and transform into felt.
The study explores the potential of wool as a bonding agent, and the felting process as a binding operation via advanced fabrication tools. The new material practice intends to form a methodology where wool is implemented in diverse scenarios, to enrich the architectural space and enhance its tangible qualities.
The project focuses on a widely used, yet rarely glorified material: wool.The organic fibre is known for its remarkable qualities. It is biodegradable, non-flammable,temperature regulating and can absorb toxic chemicals to mention but a few. The study specifically focuses on wool’s unique characteristics and investigates previously untested applications of the material.


Robotic Felting
Felting of animal hair has a versatile history of use and applications. After reviewing traditional, commercial felt manufacturing and exploring the potential of felting as a binding procedure by small-scale hand-crafted models, the next step was the translation of these findings into an automated process.
The main benefit of the transition is control. The automated process allows gathering data in a precise manner. Repeatability and accuracy were needed to conclude and extract valuable information from the felt making process. Scale and speed are two constraints that the automated process allows advancing.
The primary aim was to produce automatically, using a Universal Robot (UR10), two-dimensional felt samples. The practice allowed to map different parameters of control, extract information regarding force, speed, the number of needles and needles’ distribution.
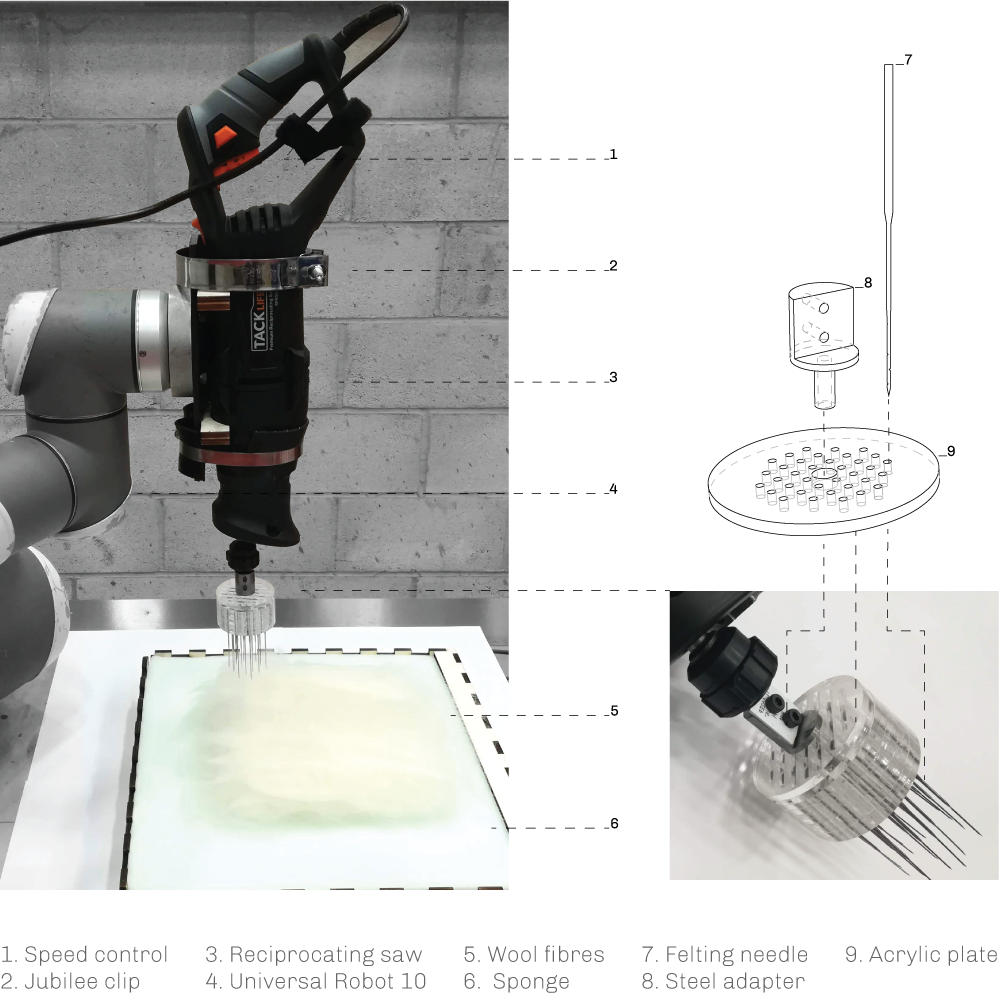
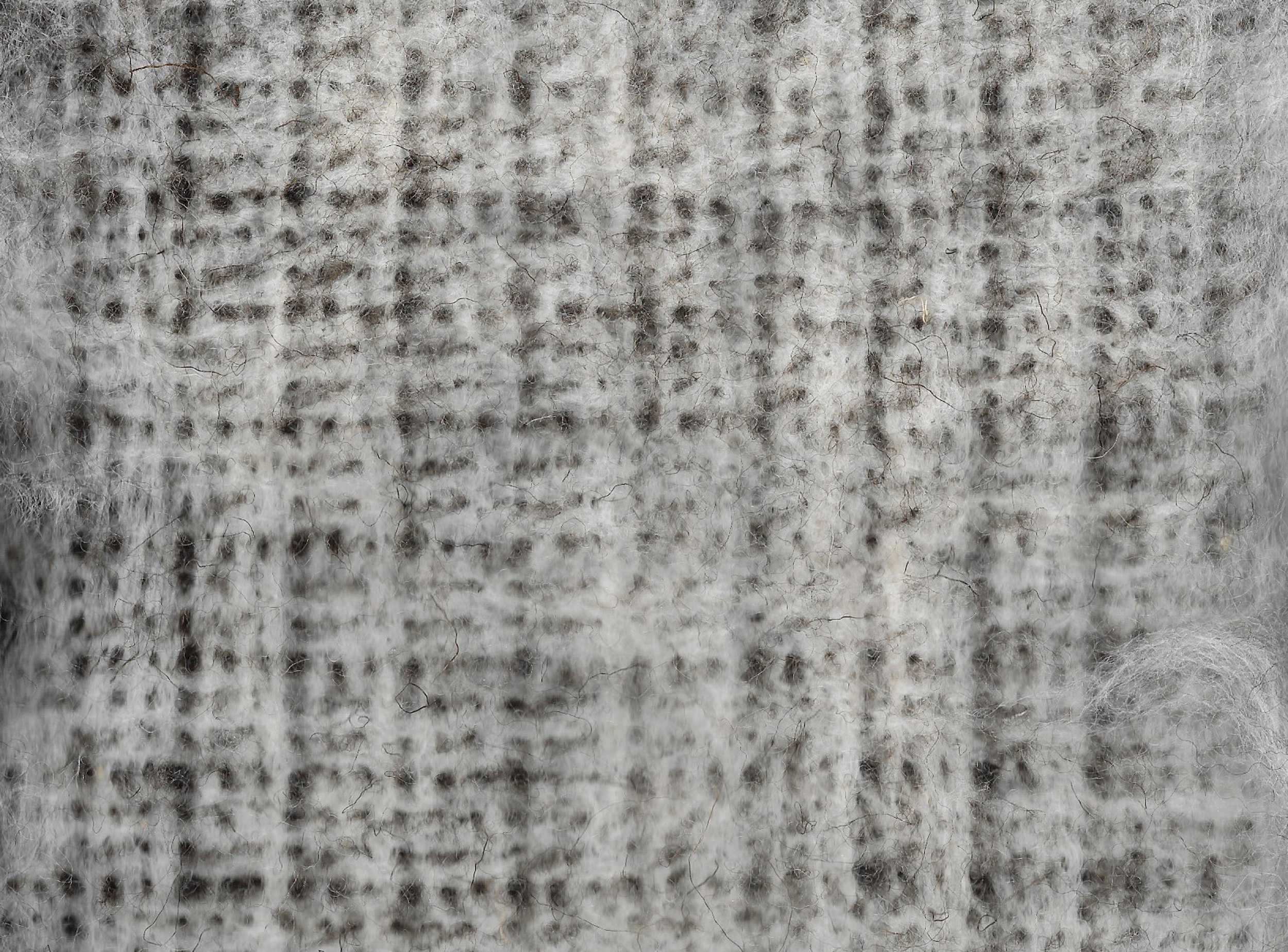


Hydroentanglement
Throughout the needle felting experiments, some challenges and limitations have risen. The study encountered an additional fabrication method. Hydroentanglement is a method based on technology developed in the late 1950s and further advanced in the US and is well established in the production of synthetic fibres in the nonwoven industry.
The method follows a similar principle of mechanical entanglement as the needle-felting process. Utilising water jets to replace the engineered needles.The presence of similar machinery in the facilities allowed investigating the new manufacturing approach.
The waterjet used for the following work does not feature the same components as the specialised machinery used for the hydroentanglement process. The first trial included a fibrous web, also named batt and a piece of MDF that served as backing. The board was needed since the waterjet machine has a grill like structure, not a solid bed. The batt was secured with a polyester knit mesh, stretched and fixed to the board, to prevent the fibres movement during the process.
The outcome was a complete surprise. Instead of felting the fibres with themselves, the machine pushed the wool fibres deep into the MDF. The result was different from the expectations, but it opened a door for further investigation.
The outcome was a complete surprise. Instead of felting the fibres with themselves, the machine pushed the wool fibres deep into the MDF. The result was different from the expectations, but it opened a door for further investigation.


Soft Joinery
The waterjet process allows embedding wool fibres into rigid materials. Even though it does not condense and transform the wool fibres into felt the qualities of the composite achieved by the procedure were of interest.
The study included the sampling of numerous backing materials such as plastics, metal meshes, plywood and hardwoods in addition to testing various joinery strategies. One path was flat wool ‘seams’ that form soft, flexible joints. Another trajectory was the exploration of three-dimensional wool connections, that allow fixing plywood members in predefined angles.
Since the waterjet is a 3-axis machine, the production of three-dimensional joints required the aid of a substructure and was limited in scale. The manufacturing method developed throughout the project offers a new perspective regarding the introduction of soft materials into the architectural space. As part of the study the Spatial Felted Structure was produced as a demonstrator model.

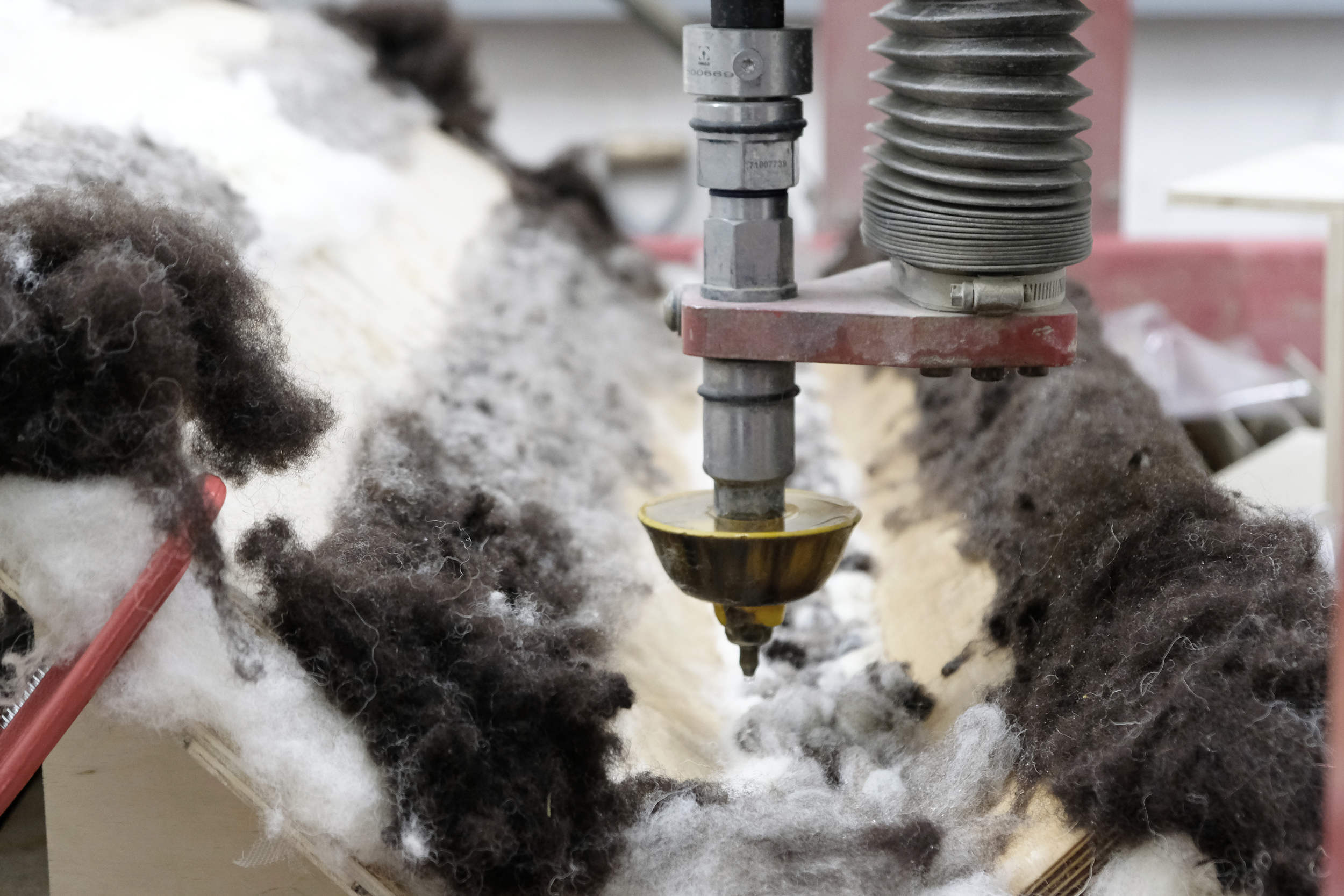
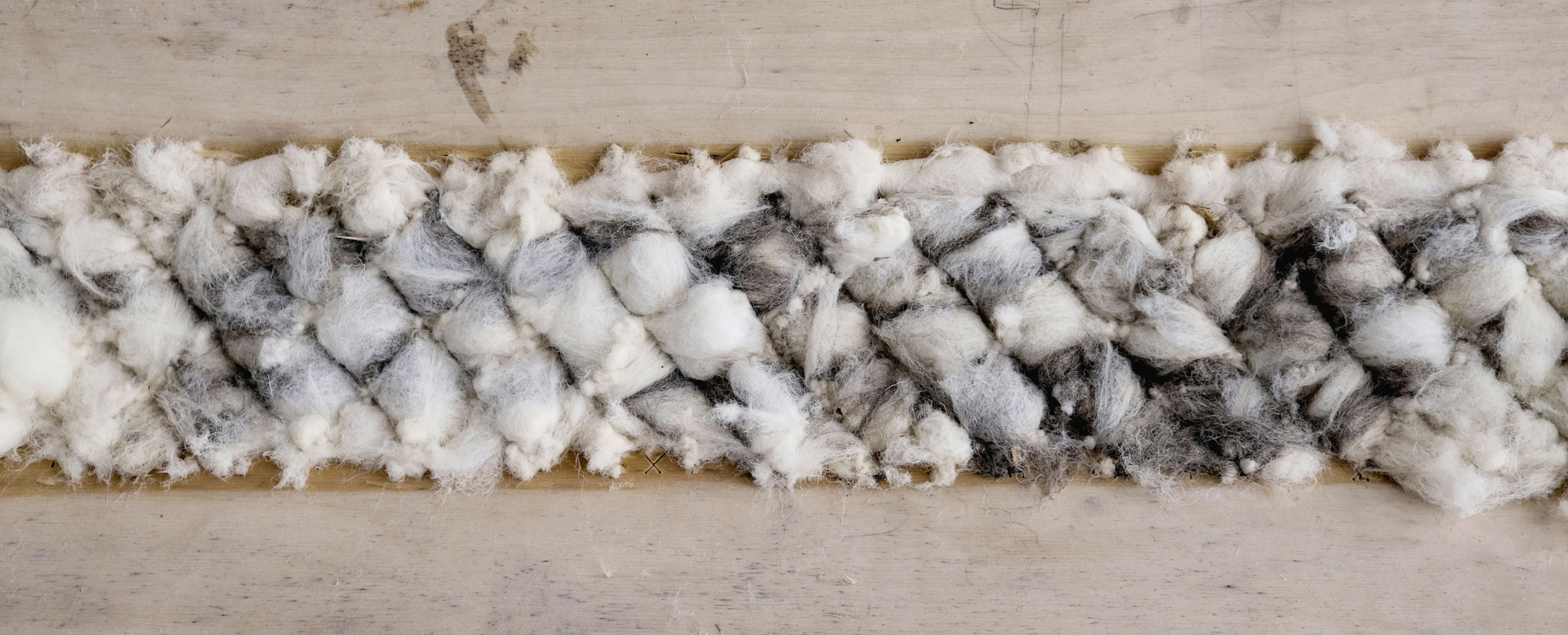